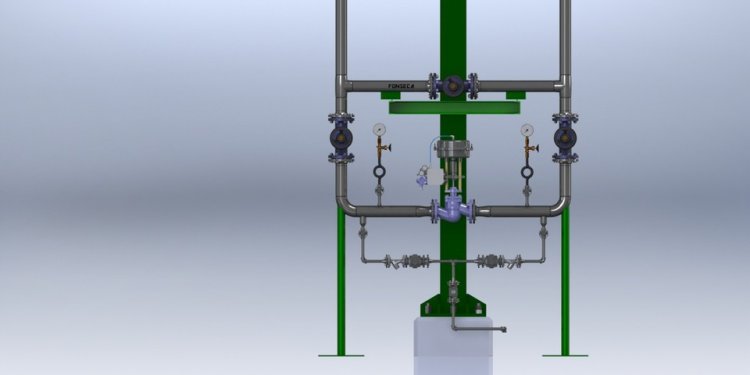
Design Engineer Interview questions
1.What are the different types of fits? Explain?
2. What are the factors that can affect the Factor of safety selection?
3. What is heat treatment and why is it done?
4. What are the rules that must be kept in mind while designing castings?
5. What are the points that should be kept in mind during forging design?
6. Describe briefly the different cold drawing processes.
7. What are the different theories of failure under static load, explain briefly?
What are the different types of fits? Explain?
On the basis of Indian standards fits can mainly be categorized into three groups:
Clearance Fit: These types of fits are characterized by the occurrence of a clearance between the two mating parts. The difference between the minimum size of the hole and the maximum size of the shaft is called the minimum clearance, the difference between the maximum size of the hole and the minimum size of the shaft is known as maximum clearance.
Interference Fit: In these types of fits the size of the mating parts are predefined so that interference between them always occurs. The tolerance zone of the hole is completely below the tolerance zone of the shaft.
Transition Fit: As the name suggests these type of fit has its mating parts sized limited to allow either clearance or interference. The tolerance zone of the hole and the shaft overlaps in case of such fits.
For a shaft designated as 40 H8/f7, calculate the tolerances.
Given: Shaft designation = 40 H8/f7
The shaft designation 40 H8/f 7 means that the basic size is 40 mm and the tolerance grade for
the hole is 8 ( i. e. I T 8) and for the shaft is 7 ( i. e. I T 7).
Since 40 mm lies in the diameter steps of 30 to 50 mm, therefore the geometric mean diameter,
D = Square root of (30 x 50) = 38.73 mm
We know that standard tolerance unit,
i = 0.45 x Cube root of (D) + 0.001 D
i = 0.45 × 3.38 + 0.03873 = 1.559 73 or 1.56 microns
i = 1.56 × 0.001 = 0.001 56 mm ...(1 micron = 0.001 mm)
The standard tolerance for the hole of grade 8 (IT8)
= 25 i = 25 × 0.001 56 = 0.039 mm
The standard tolerance for the shaft of grade 7 (IT7)
= 16 i = 16 × 0.001 56 = 0.025 mm
What are the factors that can affect the Factor of safety selection?
The factor of safety is used in designing a machine component. Prior to selecting the correct factor of safety certain points must be taken into consideration such as:
The properties of the material used for the machine and the changes in its intrinsic properties over the time period of service.
The accuracy and authenticity of test results to the actual machine parts.
The applied load reliability.
The limit of stresses (localized).
The loss of property and life in case of failures.
The limit of initial stresses at the time period of manufacture.